
Waste atau sampah dalam konteks pengendalian biaya material proyek berarti sisa material yang sudah tidak dapat dipakai lagi. Pada proyek gedung, waste material ini merupakan masalah yang sangat penting. Pelaku konstruksi sering tidak menyadari betapa waste ini telah membuat biaya proyek menjadi tidak terkendali sehingga terjadi pembengkakan biaya atau cost overrun. Mengenai berapa besaran waste itu sendiri, di Indonesia belum pernah diteliti secara spesifik. Sebagai gambaran, diberikan data suatu penelitian yang dilakukan oleh Farmoso, C.T. dalam Journal of Construction Engineering and Management.
No. | Lokasi Penelitian | Sampling | Tahun | Nilai Waste |
1. | Inggris | 114 proyek | 1960 – 1970 | 2% – 15% |
2. | Hongkong | 32 proyek | 1992 – 1993 | 2,4% – 26,5% |
3. | Belanda | 5 proyek | 1993 – 1994 | 1% – 10% |
4. | Australia | 15 proyek | N/A | 2,5% – 22% |
5. | Brazil | 3 proyek | 1986 – 1987 | 11% – 17% |
Hasil penelitian di atas, menunjukkan bahwa nilai waste dapat mencapai >25%. Suatu nilai yang tidak terduga yang pasti akan membuat biaya pelaksanaan proyek naik cukup tinggi. Umumnya dalam proyek gedung, material besi beton merupakan material yang memiliki prosentase terhadap biaya tertinggi yaitu berkisar 20% – 25%. Sehingga perhatian pada pengendalian waste besi beton pada proyek gedung menjadi layak untuk dilakukan. Jika prosentase material besi adalah 25% dan terjadi waste sebesar 10% sedangkan nilai proyek dianggap Rp. 100 Milyar, maka terjadi over budget sebesar 10% x 25% x 100 M = 2.5 Milyar atau 2.5% terhadap Nilai Kontrak. Cukup fantastis bukan?
Secara teori, waste of material terbagi dalam dua kategori yaitu Direct Waste berupa sisa material yang timbul diproyek karena hilang, rusak, dan tidak dapat dipakai lagi dan Indirect Waste berupa sisa material yang terjadi di proyek karena volume pemakaian melebihi volume yang direncanakan, sehingga tidak terjadi sisa material secara fisik di lapangan dan mempengaruhi biaya keseluruhan (hidden cost). Berdasarkan teori ini, maka dapat disimpulkan bahwa umumnya waste besi tulangan merupakan indirect waste.
Besi tulangan merupakan material yang berfungsi struktural dan material yang bersama-sama dengan beton menjadi beton bertulang yang berfungsi struktural untuk menopang beban bangunan. Besi tulangan diproduksi dalam bentuk batangan dengan panjang standar 12 m. Dalam pelaksanaannya, besi tulangan dipotong-potong sesuai desain gambar struktur. Besi tulangan utuh yang dipotong-potong menjadi potongan besi lebih kecil berdasarkan desain gambar umumnya akan menghasilkan sisa hasil potongan/waste karena sisa potongan tersebut sudah tidak dapat terpakai lagi. Berikut diberikan contoh dua pola pemotongan besi tulangan:
Pada suatu bagian struktur bangunan, diperlukan potongan tulangan sesuai tabel.
Panjang potongan (cm) | Jumlah potongan | Total (cm) | Total (Btg) |
600 | 4 | 2400 | |
400 | 6 | 2400 | |
300 | 8 | 2400 | |
Jumlah | 18 | 7200 | 6 |
Untuk mendapatkan potongan besi tulangan di atas, dilakukan pemotongan terhadap besi tulangan utuh 12 m dalam dua cara/pola pemotongan, yaitu: Cara pola potong 1:2 btg besi tulangan dipotong 2 → 600-600, sisa 0 2 btg besi tulangan dipotong 3 → 400-400-400, sisa 0 2 btg besi tulangan dipotong 4 → 300-300-300-300, sisa 0 *) ukuran potongan dalam satuan cm. Cara / pola potong ini ditabelkan sebagai berikut:
Waste cara pola potong 1 = 0% Cara pola potong 2 : 4 btg besi tulangan dipotong 2 → 600-400, sisa 200 (4 btg) = 800 1 btg besi tulangan dipotong 3 → 400-400-300, sisa 100 (1 btg) = 100 1 btg besi tulangan dipotong 4 → 300-300-300-300, sisa 0 1 btg besi tulangan dipotong 3 → 300-300-300, sisa 300 (1 btg) = 300 *) ukuran potongan dalam satuan cm. Cara/pola potong ini ditabelkan sebagai berikut:
Cara Pola Potong 1 | Panjang (cm) | Jmh sisa (cm) | |||
Batang ke | Pot. 1600 cm | Pot. 2400 cm | Pot. 3300 cm | ||
1-2 | 2 | 0 | 0 | 2400 | 2×0 |
3-4 | 0 | 3 | 0 | 2400 | 2×0 |
5-6 | 0 | 0 | 4 | 2400 | 2×0 |
Jumlah | 4 pot. | 6 pot. | 8 pot. | 7200 | 0 |
Waste cara pola potong 2 = 1200 / 7200 = 16,7%. Dua cara potong di atas menghasilkan nilai waste yang berbeda. Cara potong yang pertama menghasilkan waste 0%, sedangkan cara pola potong ke-2 menghasilkan waste 16,7%. Hal ini berarti beda cara/pola potong maka kemungkinan memberikan nilai waste yang berbeda. Ketidaktelitian membuat waste makin besar.
Mari kita telusuri lebih jauh. Dalam praktiknya saat ini pelaksana proyek menentukan pola potong berdasarkan prinsip pendekatan dimana panjang potongan-potongan besi dipadankan sedemikian rupa hingga tidak ada sisa atau sisa sekecil mungkin saat memotong besi tulangan utuh. Contoh untuk mengilustrasikan prinsip pemotongan di atas adalah sebagai berikut:
- 600-600, 500-700, 400-800, 200-1000, 100-1100, dan seterusnya.
- 200-400-600, 300-400-500, 400-400-400, 500-500-200, dan seterusnya.
- 200-300-300-400, 100-300-400-400, 200-200-300-500, 200-200-400-400, dan seterusnya.
Dalam setiap kali menentukan pola pemotong, cara potong tersebut dilakukan terlebih dulu. Pelaksana terlebih dulu mendata data ukuran potongan yang mungkin akan dapat berpadanan sehingga membentuk pola yang menghasilkan total panjang 12 m. Cara potong ini, pada dasarnya cukup efektif untuk ukuran proyek yang kecil dan tidak komplek elemen strukturnya. Namun dengan cara ini sebenarnya waste tulangan belumlah optimum. Ada baiknya untuk melihat studi kasus berikut ini.
Pada suatu bagian struktur bangunan, diperlukan potongan tulangan sesuai tabel.
Panjang potongan (cm) | Jumlah potongan | Total (cm) | Total (Btg) |
300 | 8 | 2400 | |
400 | 16 | 6400 | |
750 | 16 | 12000 | |
850 | 8 | 6800 | |
Jumlah | 48 | 27600 | 23 |
Pada kasus di atas, diperlukan total 48 potongan dengan panjang besi tulangan teoritis 23 batang. Berikut adalah ilustrasi pola potong yang terjadi selama ini oleh pelaksana di proyek dan cara / pola potong terbaik yang mungkin.
Cara/pola potong Pelaksana/Existing:
Cara / Pola Potong Pelaksana / Existing | Sisa (cm) | ||||
Batang ke | Pot. 1 300cm | Pot. 2 400cm | Pot. 3 750cm | Pot. 4 850cm | |
1-5=5 btg | 0 | 3 | 0 | 0 | 5x(1200-3×400)=0 |
6-7=2 btg | 4 | 0 | 0 | 0 | 2x(1200-4×300)=0 |
8=1 btg | 0 | 1 | 1 | 0 | 1x(1200-400-750)=50 |
9-16=8 btg | 0 | 0 | 0 | 1 | 8x(1200-850)=2800 |
17-31=15 btg | 0 | 0 | 1 | 0 | 15x(1200-750)=6750 |
Jumlah | 8 pot. | 16 pot. | 16 pot. | 8 pot. | 9600 |
Waste cara pola potong Pelaksana / Existing = 9600 / 27600 = 34,78% Cara/pola potong terbaik:
Cara / Pola Potong Pelaksana / Existing | Sisa (cm) | ||||
Batang ke | Pot. 1 300cm | Pot. 2 400cm | Pot. 3 750cm | Pot. 4 850cm | |
1-8=8 btg | 1 | 0 | 0 | 1 | 8x(1200-300-750)=400 |
9-23=16 btg | 0 | 1 | 1 | 0 | 16x(1200-400-850)=800 |
Jumlah | 8 pot. | 16 pot. | 16 pot. | 8 pot. | 1200 |
Waste cara pola potong Pelaksana / Existing = 1200 / 27600 = 4,35%.
Pada kasus di atas ternyata cara yang dilakukan saat ini oleh pelaksana terbukti masih belum optimal. Contoh ini mungkin terlalu sederhana (simulasi 48 potongan dengan 4 variasi ukuran potongan) dimana pada kenyataannya jumlah potongan yang dibuat di proyek jauh lebih besar dan dapat mencapai ribuan potong besi tulangan dengan variasi ukuran potongan mencapai puluhan variasi. Tapi cukup untuk membuktikan bahwa ada cara lain yang lebih baik.
Tentu ini bukan pekerjaan mudah untuk melakukan trial simulasi pola/cara potong sehingga didapatkan simulasi yang terbaik untuk mendapatkan waste tulangan yang optimal apalagi oleh pelaksana di lapangan dimana terdapat ribuan potong tulangan yang harus ditrial. Dibutuhkan waktu yang sangat lama untuk mendapatkan pola/cara potong yang terbaik. Perlu sebuah software untuk memudahkan pekerjaan ini.
Itulah awal dari terciptanya Software Optimasi Waste Besi (SOWB). SOWB dibuat dengan berdasarkan cara kerja pendekatan matematika algoritma yang dirancang untuk membantu mendapatkan cara pola potong yang optimal. Software ini dibangun dengan bahasa visual basic yang diimplant ke dalam microsoft excel. Digunakannya microsoft excel agar memudahkan dalam proses editing output yang mungkin cukup banyak agar siap untuk digunakan. Ide untuk menggunakan algoritma matematika merupakan ide yang akan menghasilkan pola potong dengan waste yang paling minimum yang mungkin dari sekian banyak pola potong yang mungkin terjadi. Sementara ini, software tampil dalam bentuk yang cukup sederhana karena lebih mementingkan fungsi yang didapat. Berikut tampilan bagian input dan bagian output dari SOWB tersebut.
Tampilan Input
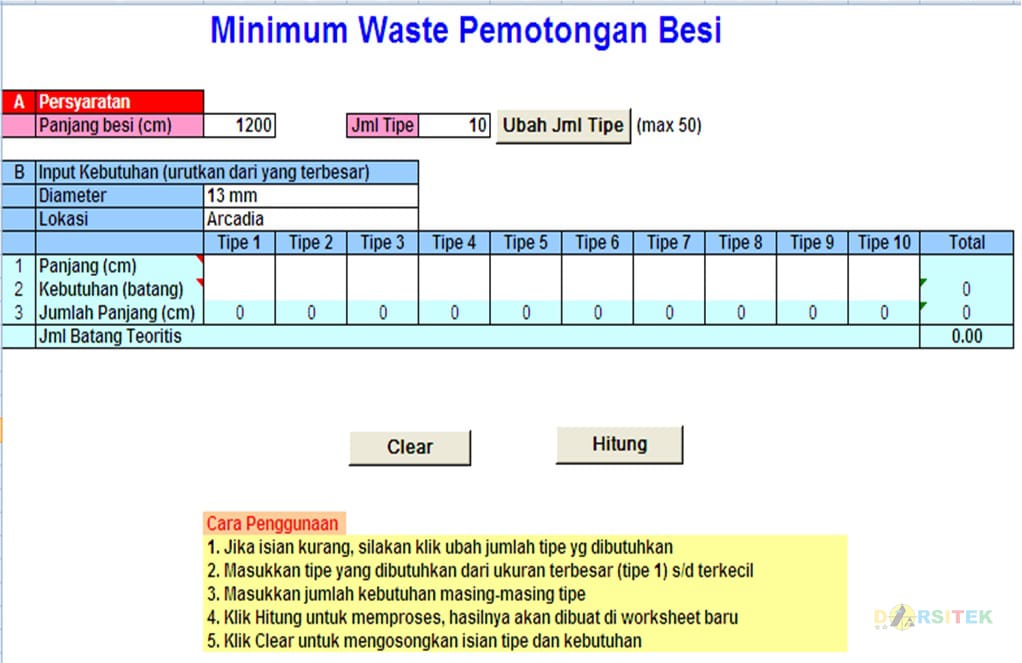
Tampilan Output

Di Internet, anda dapat membeli software serupa. Cukup cari di google search dengan keyword rebar cutting optimization. Di sana juga terdapat beberapa software yang free for trial. Darsitek akan berikan linknya disini => Rebar Cutting software Free Trial, Anda dapat mencoba untuk membandingkan hasilnya secara manual dengan software tersebut.
Sekian artikel kali ini, mudah-mudahan bisa bermanfaat untuk kita semua. Jangan lupa share artikel ini ke sosial media atau jika ingin terus mengikuti perbaruan konten situs ini, silahkan subscribe pada notifikasi yang muncul saat pertama kali mengakses situs ini. Sekian dan terimakasih.